「溶接作業を導入したいけど、安全面が心配…」
「どんなリスクがあって、どう対策すれば良いんだろう?」
「必要な保護具や注意点を体系的に知りたい」
こんにちは!初めて溶接作業を会社に導入しようとしている安全担当者の皆さん、上記のような悩みを抱えていませんか?
溶接は製造業や建設業において欠かせない技術ですが、その一方で感電や火災、やけどなど様々なリスクが伴います。
本記事では、溶接作業に伴う主要なリスクとその評価方法、具体的な対策までを分かりやすく解説します。
この記事を読めば、溶接作業の安全管理に必要な知識が身につき、現場の安全を確保するための第一歩を踏み出せるでしょう。
溶接作業とは?基本的な種類と特徴
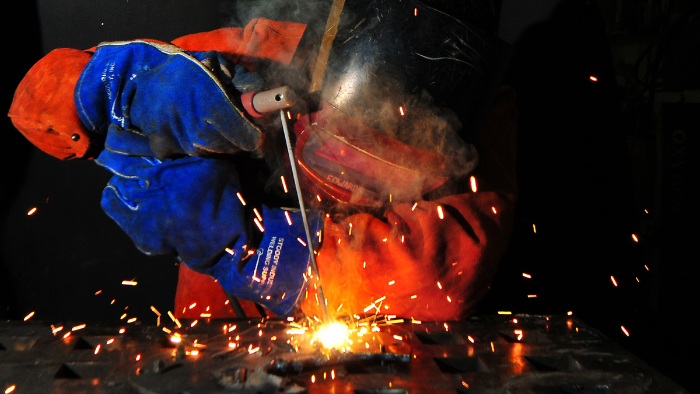
溶接作業を安全に行うためには、まずどのような種類の溶接があるのかを理解しておく必要があります。
それぞれの溶接方法によって、リスクの性質や大きさが異なるからです。
主な溶接の種類
- アーク溶接
- 電極と母材の間にアークを発生させて熱で金属を溶かす方法
- 代表例:被覆アーク溶接、TIG溶接、MIG/MAG溶接など
- 特徴:高温、強い紫外線、スパッタ(飛散する金属粒)の発生
- ガス溶接
- 酸素とアセチレンなどの可燃性ガスを燃焼させて金属を溶かす方法
- 特徴:火災リスクが高い、有害ガスの発生
- 抵抗溶接
- 電気抵抗による発熱を利用して金属を溶接する方法
- 代表例:スポット溶接、シーム溶接
- 特徴:比較的安全だが、感電リスクは存在
- レーザー溶接
- レーザービームを用いて金属を溶接する方法
- 特徴:高精度だが、目への危険性が高い
それぞれの溶接方法には固有のリスクがありますが、本記事ではより一般的なアーク溶接を中心にリスクアセスメントを解説していきます。
溶接作業におけるリスクアセスメントの重要性
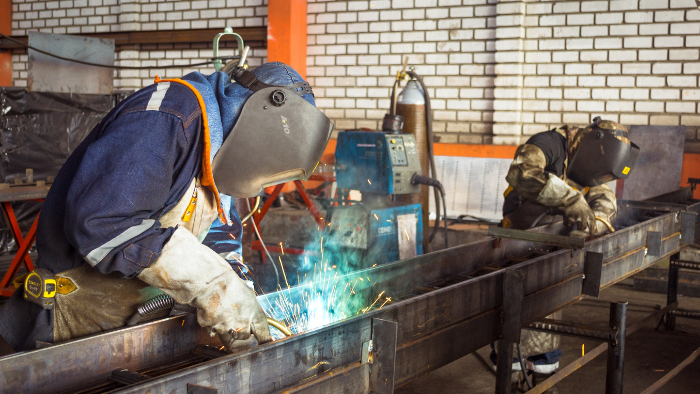
リスクアセスメントとは、作業に伴う危険性や有害性を特定し、リスクの大きさを評価した上で適切な対策を講じるプロセスです。
溶接作業では以下の理由からリスクアセスメントが特に重要となります
- 複数の危険要因(電気、熱、光、煙、ガスなど)が同時に存在する
- 事故が発生した場合の被害が重大になる可能性がある
- 作業環境や条件によってリスクの大きさが変化する
それでは、溶接作業における主要なリスクとその対策について詳しく見ていきましょう。
溶接作業の主なリスクと対策
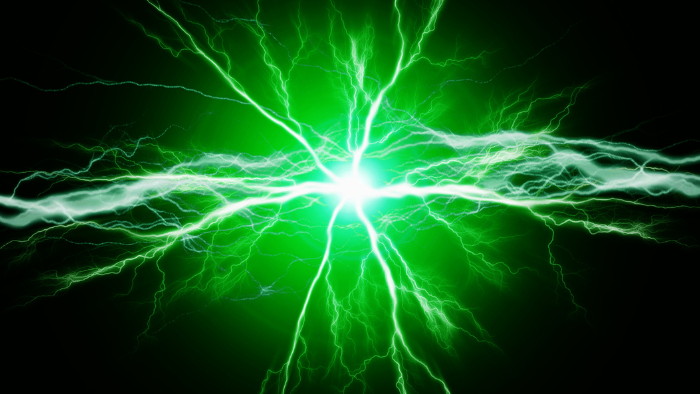
1. 感電・漏電リスク
溶接作業、特にアーク溶接では高電流を使用するため、感電や漏電のリスクは非常に高いと言えます。
リスク要因
- 絶縁不良の溶接機や電線
- 濡れた床や手袋での作業
- 狭い金属製の空間での作業
- 不適切なアース(接地)
対策
- 溶接機の定期点検:絶縁抵抗測定や外観検査を定期的に実施
- 漏電遮断器の設置:感電事故防止の最後の砦として必須
- 乾燥した作業環境の確保:濡れた場所での作業は避ける
- 絶縁手袋の着用:特に高湿度環境では重要
- 適切なアース接続:溶接対象物に確実にアースを取る
- 作業前の点検:ケーブルの損傷やプラグの状態を毎回確認
2. 火傷(やけど)リスク
溶接時の温度は数千度に達するため、火傷は最も一般的な傷害の一つです。
リスク要因:
- 高温の母材や溶接部に触れる
- スパッタ(飛び散る溶融金属粒)
- 熱伝導による間接的な加熱
- 保護具の不備
対策
- 適切な保護具の着用:耐熱性の作業着、手袋、安全靴
- 冷却時間の確保:溶接後の金属が十分に冷えるまで触れない
- 作業区域の明示:高温部があることを周囲に警告
- ピンセットや工具の活用:直接手で触れる機会を減らす
- スパッタ防止シートの使用:飛散防止と周囲の保護
3. 火災リスク
溶接作業では高温の火花や金属粒が飛散するため、火災リスクも高いです。
リスク要因
- 可燃物の近くでの作業
- スパッタの飛散
- 隠れた場所への火の粉の侵入
- 不適切な消火設備
対策
- 作業場所の整理整頓:可燃物の除去と安全距離の確保
- 防火シートの設置:床や周囲の保護
- 消火器の設置:種類と数の適正化
- 火気監視人の配置:特に危険度の高い場所での作業時
- 作業後の点検:火種が残っていないか確認
- ホットワーク許可制度の導入:火気使用前の安全確認プロセスの確立
4. 目の傷害リスク
溶接アークからは強力な紫外線や赤外線が発生し、目の傷害(電光性眼炎)を引き起こす可能性があります。
リスク要因:
- 強い紫外線・赤外線への直接曝露
- 不適切な保護具
- 反射光による間接的な曝露
- 周囲の作業者への影響
対策
- 適切な遮光度の溶接面の使用:JIS規格に基づいた選定
- 側面からの光も防ぐ設計の保護具選択
- 自動遮光溶接面の採用:作業効率と安全性の両立
- 作業区域の囲い:カーテンや衝立で周囲への影響を防止
- 定期的な目の検診:早期発見と対処
5. スパッタによるリスク
スパッタとは溶接時に飛び散る高温の金属粒のことで、火傷や火災の原因となります。
リスク要因:
- 不適切な溶接条件
- 保護具の不備
- 周囲の可燃物
- 飛散範囲の認識不足
対策
- 適切な溶接条件の設定:電流や速度の最適化
- スパッタ低減ワイヤの使用:可能な場合
- スパッタ防止スプレーの活用
- 防護衝立や防火シートの設置
- 長袖・長ズボンの難燃性作業服の着用
6. 有害光線・ヒュームによるリスク
溶接作業では有害な光線や煙(ヒューム)が発生し、健康被害を引き起こす可能性があります。
リスク要因
- 金属ヒュームの吸引
- 紫外線への長期曝露
- 換気不良の密閉空間での作業
- 特定金属(亜鉛、クロム、マンガンなど)の溶接
対策:
- 局所排気装置の設置:発生源での吸引
- 全体換気の確保:作業場の空気の入れ替え
- 呼吸用保護具の着用:状況に応じた適切な選択
- 定期的な健康診断:ヒューム曝露の影響チェック
- 作業時間の管理:過度の曝露を避ける
溶接作業に必要な保護具一覧
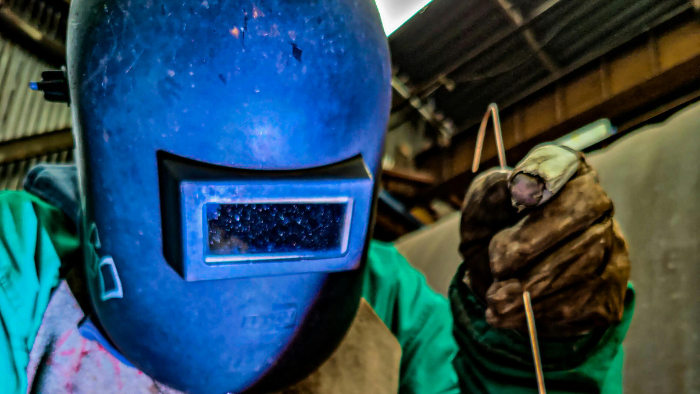
溶接作業を安全に行うためには、適切な保護具の選定と使用が不可欠です。以下に主要な保護具を紹介します。
1. 頭部・顔面の保護
- 溶接面:紫外線・赤外線から目を保護(JIS規格の適切な遮光度を選択)
- 自動遮光溶接面:作業効率向上と安全性確保の両立
- 安全ヘルメット:落下物からの保護(溶接用頭巾と併用)
2. 呼吸器の保護
- 防じんマスク:ヒュームから呼吸器を保護
- 電動ファン付き呼吸用保護具:長時間作業時の快適性と安全性の確保
- 送気マスク:密閉空間での作業時
3. 身体の保護
- 難燃性作業服:長袖・長ズボンで全身を覆う
- 溶接用エプロン:前面の強化保護
- 溶接用腕カバー・足カバー:スパッタからの保護
4. 手の保護
- 耐熱手袋:高温の溶接部やスパッタからの保護
- 電気絶縁手袋:感電防止(必要に応じて)
5. 足の保護
- 安全靴:スパッタや落下物からの保護
- 足カバー:靴の上からスパッタを防ぐ
効果的なリスクアセスメントの実施方法
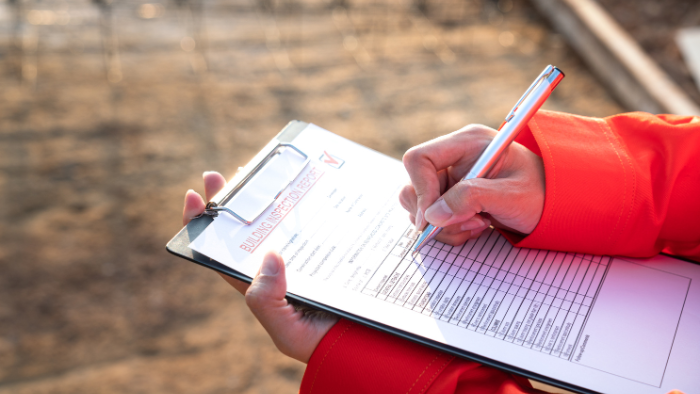
溶接作業のリスクアセスメントを効果的に行うためのステップを解説します。
Step 1: 作業の洗い出し
- 溶接前準備、本溶接作業、後処理など工程ごとに分ける
- 作業環境(屋内/屋外、高所、密閉空間など)も考慮
Step 2: 危険源の特定
- 電気的危険(感電、漏電)
- 熱的危険(火傷、火災)
- 光学的危険(紫外線、赤外線)
- 化学的危険(ヒューム、ガス)
- 物理的危険(騒音、振動、姿勢)
Step 3: リスクの見積り
- 発生可能性(頻度)の評価
- 被害の重大性の評価
- リスクレベルの算出(リスクマトリクスの活用)
Step 4: リスク低減対策の検討
- 本質的対策:危険源の除去や代替
- 工学的対策:ガード、インターロック、換気装置など
- 管理的対策:作業手順、教育訓練、立入禁止
- 個人用保護具:最後の砦として
Step 5: 対策実施と効果確認
- 対策の実施と記録
- 残留リスクの評価
- 必要に応じて追加対策の実施

溶接作業の安全教育ポイント
安全な溶接作業のためには、作業者への適切な教育が不可欠です。
1. 基本知識の教育
- 溶接の原理と種類
- 各溶接法の特徴とリスク
- 電気の基礎知識(アーク溶接の場合)
2. リスク認識の教育
- 潜在的な危険の理解
- リスクの大きさと発生メカニズム
- 実際の事故事例の共有
3. 実技教育
- 正しい作業姿勢と手順
- 保護具の適切な着用方法
- 緊急時の対応
4. 定期的な再教育
- 最新の安全基準の更新
- 新しい保護具や技術の紹介
- ヒヤリハット事例の共有
まとめ
溶接作業は様々なリスクを伴う作業ですが、適切なリスクアセスメントと対策により、安全に実施することが可能です。
安全管理のポイント
- 包括的なリスクアセスメント:すべての危険源を洗い出す
- 階層的な対策の実施:本質安全化から保護具まで多層的に
- 適切な保護具の選定と使用:作業内容に合わせた最適な保護
- 作業環境の整備:換気、防火、区画などの環境対策
- 継続的な教育と訓練:知識と技能の定期的な更新
- ヒヤリハット活動:小さな異常の段階での対処
- 定期的な設備点検:溶接機器やケーブルの劣化チェック
溶接作業の安全は一朝一夕に確立できるものではありません。
継続的な改善と関係者全員の安全意識が大切です。
最後までお読みいただきありがとうございました!
参考:関連法令と規格
- 労働安全衛生法:第20条(危険防止措置)、第22条(健康障害防止措置)
- 労働安全衛生規則:第320条~第327条(アーク溶接等の作業)
- 粉じん障害防止規則:第27条(溶接ヒュームに関する措置)
- JIS Z 3950:溶接用安全器具
- JIS T 8141:遮光保護具
これらの法令や規格を遵守することも、安全な溶接作業の基本となります。
コメント