「うちの現場では巻き込まれ事故なんて起こっていないから大丈夫…」そう思っていませんか?
しかし、回転体を扱う現場では、どんなに気をつけていても 着衣による巻き込まれ事故 が発生するリスクがあります。
実際に全国で発生している労働災害の中でも、巻き込まれ事故は毎年一定数報告されています。
安全レベルを向上させたいけれど、具体的に何をすれば良いのか悩んでいる安全担当者の方も多いはずです。
この記事では、巻き込まれ事故の原因から具体的な防止策、リスクアセスメントの方法までを徹底解説します。
現場の安全性向上にぜひお役立てください!
1. 巻き込まれ事故とは?
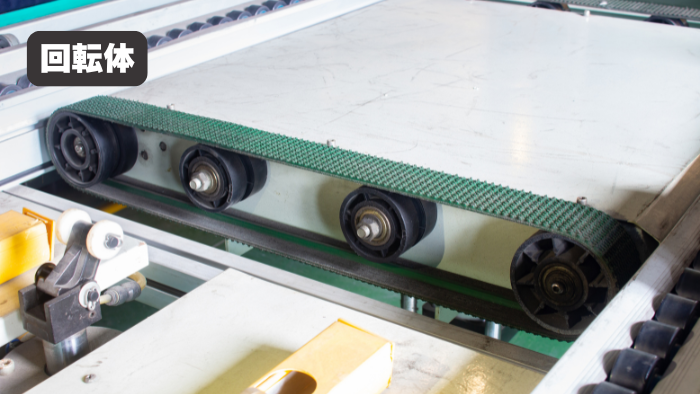
巻き込まれ事故の定義
巻き込まれ事故とは、機械や回転体の可動部分に作業者の身体や着衣が引き込まれ、重大な怪我や死亡事故につながる災害のことを指します。
主に以下のような機械で発生しやすいとされています。
- コンベヤー
- ドリル・ボール盤
- 旋盤
- ミキサー
- ファン・ブロワー
- 製粉機
- ポンプ装置
- ベルト駆動装置
着衣による巻き込まれの特徴
特に 着衣 による巻き込まれ事故は、一瞬の油断で発生します。
緩んだ袖口や開いたポケット、垂れ下がった紐が回転体に絡みつき、引き込まれてしまうケースが多発しています。
着衣のリスクが高い服装
- 長袖シャツ(袖口が締まっていないもの)
- ジャケットの裾が出ている状態
- フード付きパーカー
- エプロンの紐が垂れ下がっている場合
- スカーフやネクタイなどのアクセサリー
- 指輪やネックレスなどの装飾品
2. 巻き込まれ事故の原因
巻き込まれ事故が発生する主な原因は次の通りです。
① 作業服の不適切な着用
- 袖が長すぎる
- ファスナーやボタンを締めていない
- フード付きの服を着用している
- 装飾品の未着脱
作業服は必ず体にフィットしたものを選びましょう。
また、ポケット内の物品も取り出してから作業にあたりましょう。
② 安全装置の無効化
- 安全カバーが外されている
- 非常停止スイッチの設置が不十分
- 安全装置のメンテナンス不足
- センサー式安全装置の故障放置
- 自己判断による安全装置の解除
③ 教育不足
- 巻き込まれ事故のリスクを知らない
- 作業手順の周知不足
- 新入社員への安全教育が不足している
- 再教育の未実施
- 管理者による巡回指導の不足
3. 巻き込まれ事故の事例
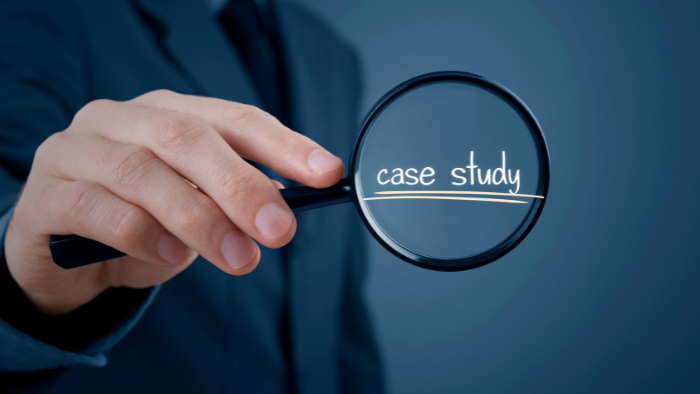
事例1: コンベヤーでの巻き込まれ
発生状況: 清掃中に作業服の袖がコンベヤーに絡まり、前腕部に重傷を負った。
原因: 作業中の機械を停止させずに清掃を行った。
事例2: 旋盤での巻き込まれ
発生状況: 作業者が旋盤で加工中、袖口が回転する部品に巻き込まれた。
原因: 袖口のボタンを締めていなかった。
事例3: ミキサーでの巻き込まれ
発生状況: 原料投入時にエプロンの紐がミキサーに巻き込まれた。
原因: エプロンの紐が垂れ下がっていた。
事例4: ポンプ装置での巻き込まれ
発生状況: 配管メンテナンス中に袖口がポンプ装置の回転部分に巻き込まれた。
原因: 袖口を固定していなかった。
4. 巻き込まれ事故の防止策
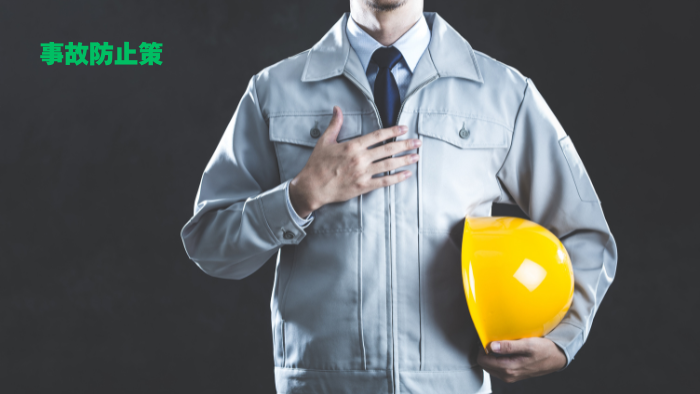
① 正しい作業服の着用
- 袖口や裾口をきちんと締める
- 紐やフード付きの服は禁止
- 専用の防護服を使用する
- 静電気防止の防護服を採用する
- マジックテープ付きの作業服を導入
- 装飾品の着用禁止を徹底
② 安全装置の徹底
- 安全カバーの設置と点検
- 非常停止スイッチの配置
- センサー式安全装置の導入
- 巻き込み防止用カバーの設置
- 定期的な安全装置の点検実施
③ 作業手順の見直し
- 機械停止後に作業を行うルールの徹底
- 指差し呼称による安全確認
- 作業前の服装点検を義務化
- 作業手順マニュアルの見直しと更新
- 管理者による安全パトロールの実施
5. 巻き込まれリスクアセスメントの手順
- リスクの洗い出し: 使用する機械と作業内容をリストアップ
- リスク評価: 巻き込まれ事故の発生頻度と影響度を評価
- 対策の優先順位付け: 高リスクな作業から優先的に対策を実施
- リスク低減措置の実施: 作業手順の変更や設備の改善
- 効果の確認と見直し: 定期的なリスクアセスメントの実施

6. まとめ
巻き込まれ事故は 未然に防ぐことができる労働災害 です。安全教育の徹底やリスクアセスメントの実施によって、安全文化の根付いた職場環境を目指しましょう。
安全担当者の皆さんの取り組みが、現場の安全性向上につながります。
安全な現場づくりを目指して、一緒に取り組んでいきましょう!
コメント